其他名称:条纹 特征:铸件表面上呈现与金属液流动方向相一致的,用手感觉得出的局部下陷光滑纹路。此缺陷无发展倾向,用抛光法能去除。
产生原因 | 排除措施 |
①两股金属流不同步充满型腔而留下的痕迹。 ②模具温度低,如锌合金模温低于 150℃,铝合金模温低于 180℃,都易产生这类缺陷。 ③填充速度太高。 ④涂料用量过多。 |
①调整内浇口截面积或位置。 ②调整模具温度,增大溢流槽。 ③适当调整填充速度以改变金属液填充型腔的流态。 ④涂料适用薄而喷匀。 |
擦伤
其他名称:拉伤、拉痕、粘模伤痕
特征:顺着脱模方向,由于金属粘附,模具制造斜度太小而造成铸件表面的拉伤痕迹,严重时称为拉伤面。
产生原因 | 排除措施 |
①型芯、型壁的铸造斜度大小或出现倒斜度。 ②型芯、型壁有压伤痕。 ③合金粘附模具。 ④铸件顶出偏斜或型芯轴线偏斜。 ⑤型壁表面粗糙。 ⑥涂料常喷涂不到。 ⑦铝合金中含铁量低于 0.6% |
①修正模具,保证制造斜度。 ②打光压痕。 ③合理设计浇注系统避免金属流对冲型芯型壁,适当降低填充速度。 ④修正模具结构。 ⑤打光表面。 ⑥涂料用量薄而均匀,不能漏喷涂料。 ⑦适当增加含铁量至适当增加含铁量至 0.6~0.8%。 |
凹陷
其他名称:缩凹、缩陷、憋气、塌边
特征:铸件平滑表面上出现凹瘪的部分,其表面呈自然冷却状态。
产生原因 | 排除措施 |
①铸件结构设计不合理,有局部厚实部位,产生热节。 ②合金收缩率大。 ③内浇口截面积太小。 ④比压低。 ⑤模具温度太高 |
①改善铸件结构,使壁厚稍为均匀,厚薄相差较大的连接处应逐步缓和过渡,消除热节。 ②选择收缩率小的合金。 ③正确设置浇注系统,适当加大内浇口的截面积。 ④增大压射力。 ⑤适当调整模具热平衡条件,采用温控装置以及冷却等。 |
气泡
其他名称:鼓泡
特征:铸件表皮下,聚集气体鼓胀所形成的泡。
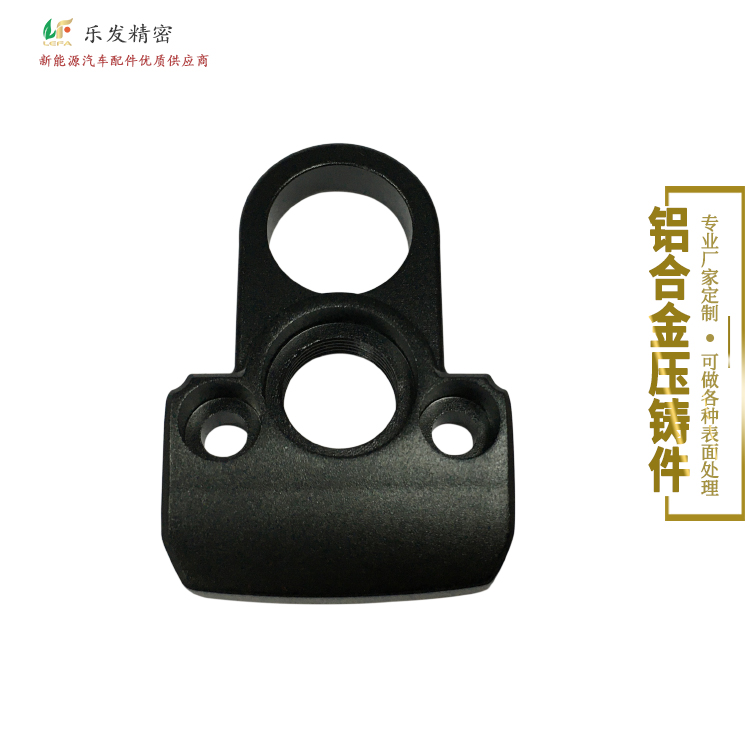
气孔
其他名称:空气孔
特征:卷入压铸件内部的气体所形成的形状较为规则,表面较为光滑的空洞。
其他名称:鼓泡
特征:铸件表皮下,聚集气体鼓胀所形成的泡。
产生原因 | 排除措施 |
①模具温度太高。 ②填充速度太高,金属液流卷入气体过多。 ③涂料发气量大,用量过多,浇注前未燃尽,使挥发气体被包在铸件表层。 ④排气不畅。 ⑤开模过早。 ⑥合金熔炼温度过高。 |
①冷却模具至工作温度。 ②降低压射速度,避免涡流包气。 ③选用发气量小的涂料,用量薄而均匀, 燃尽后合模。 ④清理和增设溢流槽和排气道。 ⑤调整留模时间。 ⑥修整熔炼工艺。 |
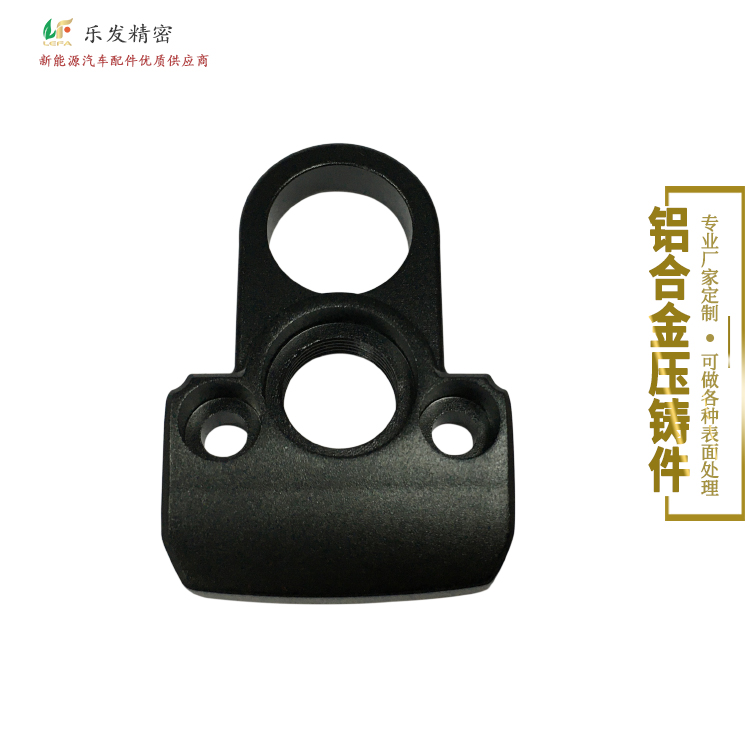
气孔
其他名称:空气孔
特征:卷入压铸件内部的气体所形成的形状较为规则,表面较为光滑的空洞。
产生原因 | 排除措施 |
主要是包卷气体引起: ①浇口位置选择和导流形状不当,导致金属液进入型腔产生正面撞击和产生旋涡。 ②浇道形状设计不良。 ③压室充满度不够。 ④内浇口速度太高,产生湍流。 ⑤排气不畅。 ⑥模具型腔位置太深。 ⑦涂料过多,填充前未燃尽。 ⑧炉料不干净,精炼不良。 ⑨机械加工余量太大。 |
①选择有利型腔内气体排除的浇口位置和导流形状,避免金属液先封闭分型面上的排溢系统。 ②直浇道的喷嘴截面积应尽可能比内浇口截面积大。 ③提高压室充满度,尽可能选用较小的压室并采用定量浇注。 ④在满足成型良好条件下,增大内浇口厚度以降低填充速度。 ⑤在型腔最后填充部位处开设溢流槽和排气道,并应避免溢流槽和排气道被金属液封闭。 ⑥深腔处开设排气塞,采用镶拼形式增加排气。 ⑦涂料用量薄而均匀,燃尽后填充,采用发气量小的涂料。 ⑧炉料必须处理干净、干燥,严格遵守熔炼工艺。 ⑨减少机械加工余量。 ⑩调整压射速度和快压射速度的转换点。降低浇注温度,增加比压。 |
欠铸
其他名称:浇不足、轮廓不清、边角残缺
特征:金属液未充满型腔,铸件上出现填充不完整的部位。
产生原因 | 排除措施 |
(1)合金液流动不良引起: ①合金液含气量高,氧化严重,以致流动性下降。 ②合金浇注温度及模具温度过低。 ③内浇口速度过低。 ④蓄能器内氮气压力不足。 ⑤压室充满度小。 ⑥铸件壁太薄或厚薄悬殊等设计不当。 (2)浇注系统不良引起: ①浇口位置,导流方式,内浇口股数选择不当。 ②内浇口截面积太小。 (3)排气条件不良引起: ①排气不畅。 ②涂料过多,未被烘干燃尽。 ③模具温度过高,型腔内气 体压力较高,不易排出。 |
(1)改善合金的流动性: ①采用正确的熔炼工艺,排除气体及非金属夹杂物。 ②适当提高合金浇注温度和模具温度。 ③提高压射速度。 ④补充氮气,提高有效压力。 ⑤采用定量浇注。 ⑥改进铸件结构,适当调整壁厚。 (2)改进浇注系统: ①正确选择浇口位置和导流方式,对不良形状铸件及大铸件采用多股内浇口为有利。 ②增大内浇口截面积或提高压射速度。 (3)改善排气条件: ①增设溢流槽和排气道,深凹型腔处可开设通气塞。 ②涂料使用薄而均匀,吹干燃尽后合模。 ③降低模具温度至工作温度。 |
网状毛刺
其他名称:网状痕迹、网状花纹、龟裂毛刺
特征:由于模具型腔表面产生热疲劳而形成的铸件表面上的网状凸起痕迹和金属刺。
产生原因 | 排除措施 |
①模具型腔表面龟裂造成的痕迹,内浇口区域附件 的热传导最集中,摩擦阻力最大,经受熔融金属的冲蚀最强,冷热交变最剧,最易产生热裂,形成龟裂。 ②模具材料不当,或热处理工艺不正确。 ③模具冷热温度变化大。 ④合金液浇注温度过高,模具预热不够。 ⑤模具型腔表面粗糙度Ra 太大。 ⑥金属流速高及正面冲刷型壁。 |
①正确选用模具材料及合理的热处理工艺。 ②模具在压铸前必须预热到工作温度范围。 ③尽可能降低合金浇注温度。 ④降低合金液浇注温度,模具预热到合适温度。 ⑤提高模具型腔表面质量,降低Ra 数值,镶块定期退火, 消除应力。 ⑥正确设计浇注系统,在满足成型良好的条件下,尽可能用较小的压射速度。 |
有色斑点
其他名称:油斑、黑色斑点
特征:铸件表面上呈现的不同于基体金属的斑点,一般由涂料碳化物形成。
其他名称:油斑、黑色斑点
特征:铸件表面上呈现的不同于基体金属的斑点,一般由涂料碳化物形成。
产生原因 | 排除措施 |
①涂料不纯或用量过多。 ②涂料中含石墨过多。 |
①涂料使用应薄而均匀,不能堆积,要用压缩空气吹散。 ②减少涂料中的石墨含量或选用无石墨水基涂 料。 |
飞边
其他名称:披缝
特征:铸件边缘上出现的金属薄片。
分层
其他名称:隔皮
特征:铸件上局部存在有明显的金属层次。
其他名称:披缝
特征:铸件边缘上出现的金属薄片。
产生原因 | 排除措施 |
①压射前机器的锁模力调整不佳。 ②模具及滑块损坏,闭锁元件失效。 ③模具镶块及滑块磨损。 ④模具强度不够造成变形。 ⑤分型面上杂物未清理干净。 ⑥投影面积计算不正确,超过锁模力。 ⑦压射速度过高,形成压力 冲击峰过高。 |
①检查合模力或增压情况,调整压射增压机构,使压射增压峰值降低。 ②检查模具滑块损坏程度并修整之,确保封锁元件起到作用。 ③检查磨损情况并修复。 ④正确计算模具强度。 ⑤清除分型面上杂物。 ⑥正确计算,调整好合模力。 ⑦适当调整压射速度。 |
分层
其他名称:隔皮
特征:铸件上局部存在有明显的金属层次。
产生原因 | 排除措施 |
①模具刚性不够,在金属液填充过程中,模板产生抖动。 ②压射冲头与压室配合不好,在压射中前进速度不平稳。 ③浇注系统设计不当。 |
①加强模具刚度,紧固模具部件。 ②调整压射冲头与压射,保证配合良好。 ③合理设计内浇口。 |
疏松
特征:铸件表面上 呈现松散不紧实的宏观组织。
错边(错扣) 其他名称:错缝
特征:铸件的一部分与另一部分在分型面上错开,发生相对位移(对螺纹称错扣)。
变形
其他名称:扭曲、翘曲
特征:铸件几何形状与设计要求不符的整体变形。
特征:铸件表面上 呈现松散不紧实的宏观组织。
产生原因 | 排除措施 |
①模具温度过低。 | ①提高模具的温度之工作温度。 |
②合金浇注温度过低。 | ②适当提高合金浇注温度。 |
③比压低。 | ③提高比压。 |
④涂料过多。 | ④涂料薄而均匀。 |
错边(错扣) 其他名称:错缝
特征:铸件的一部分与另一部分在分型面上错开,发生相对位移(对螺纹称错扣)。
产生原因 | 排除措施 |
①模具镶块位移。 ②模具导向件磨损。 ③两半模的镶块制造误差。 |
①调整镶块,加以紧固。 ②更换导柱,导套。 ③进行修整,消除误差 |
变形
其他名称:扭曲、翘曲
特征:铸件几何形状与设计要求不符的整体变形。
产生原因 | 排除措施 |
①铸件结构设计不良,引起不均匀的收缩。 ②开模过早,铸件刚性不够。 ③铸件斜度太小。 ④取置铸件的操作不当。 ⑤堆放不合理或去除浇口方法不当。 ⑥推杆位置布置不当。 |
①改进铸件结构,使壁厚均匀。 ②确定最佳开模时间,加强铸件刚性。 ③放大铸造斜度。 ④取放铸件应小心轻取轻放。 ⑤铸件堆放应用专用箱,去除浇口方法应恰当。 ⑥有的变形铸件可经整形消除 |
碰伤
特性:铸件表面因撞击而造成的伤痕。
特性:铸件表面因撞击而造成的伤痕。
产生原因 | 排除措施 |
去浇口,清理,校正和搬运 流转过程中不小心碰伤。 |
清理铸件要小心,存放及搬运铸件,不应堆 叠或互相撞击,采用专用存放运输箱。 |
脆性
特征:铸件基本金属晶粒过于粗大或细小,铸件易断裂或碰碎。
渗漏
特征:压铸件经试验产生漏水、漏气或渗水
化学成分不符合要求
特征:经化学分析,铸件合金元素不符要求或杂质过多。
特征:铸件基本金属晶粒过于粗大或细小,铸件易断裂或碰碎。
产生原因 | 排除措施 |
①合金液过热过大或保温时间过 | ①合金不宜过热,避免合金长时间保 |
长。 | 温。 |
②激烈过冷,结晶过细。 | ②提高模具温度,降低浇注温度。 |
③铝合金中杂质锌、铁等含量太 | ③严格控制合金化学成分。 |
多。 | ④保证坩埚涂料层完整良好。 |
④铝合金中含铜量超出规定范围。 |
渗漏
特征:压铸件经试验产生漏水、漏气或渗水
产生原因 | 排除措施 |
①压力不足。 | ①提高比压。 |
②浇注系统设计不合理或铸件结构不合 | ②改进浇注系统和排气系统。 |
理。 | ③选用良好合金。 |
③合金选择不当。 | ④尽量避免加工。 |
④排气不良。 | ⑤铸件进行浸渍处理。 |
化学成分不符合要求
特征:经化学分析,铸件合金元素不符要求或杂质过多。
产生原因 | 排除措施 |
①配料不正确。 ②原材料及回炉料未加分析即行投入使用。 |
①炉料应经化学分析后才能配用。 ②炉料应严格管理,新旧料要按一定比例配用。 ③严格遵守熔炼工艺。 ④熔炼工具应刷涂料。 |
机械性能不符合要求
特征:铸件合金的机械强度、延伸率低于要求标准。
产生原因 | 排除措施 |
①合金化学成分不符标准。 ②铸件内有气孔、缩孔、夹渣等。 ③对试样处理方法不对等。 ④铸件结构不合理,限制了铸件达到标准。 ⑤熔炼工艺不当。 |
①配料、熔化要严格控制化学成分及杂质含量。 ②严格遵守熔炼工艺。 ③按要求做试样,在生产中要定期对铸件进行工艺性试验。 ④改进铸件结构。 ⑤严格控制合金熔炼温度和浇注温度,尽量消除合金形成氧化物的各种因素。 |
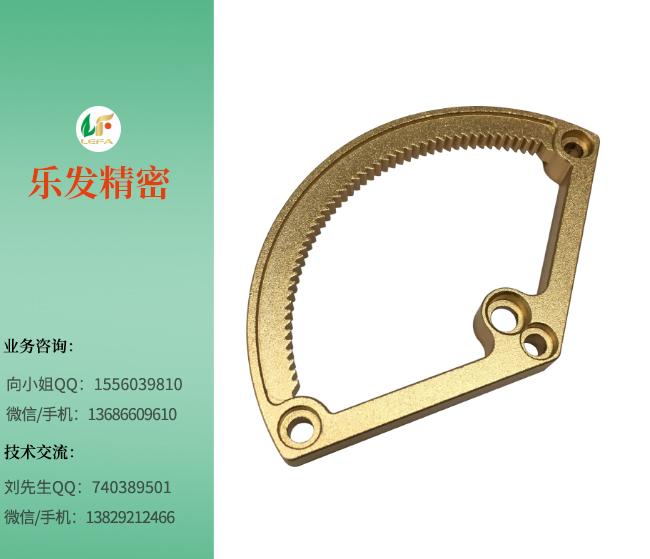
东莞市乐发精密五金制品有限公司
专注多年从事精密锌合金压铸,铝合金压铸,镁合金压铸,铜压铸生产加工及锌合金压铸模具,铝合金压铸模具,镁合金模具压铸,铜压铸模具设计与开发。拥有各种主要精密压铸加工设备具备多名高素质的工程人员我司产品主要运用领域:电子,电器,机械,数码,光学,新能源汽车,充电桩,动车组,摩托车,电瓶车,LED配件,家具,卫浴,工艺品等行业,
产品质量优势:压铸成品密度均匀,產品不易断裂、变形、重量稳定、表面均匀光滑,CNC加工、鑚孔攻牙、孔内研磨、振动研磨以及手工拋光研磨、各种色泽电镀、阳极处理、奈米烤漆、电镀、非铬酸皮膜处理(符合ROHS、WEEE环保要求,產品耐腐蚀及中性盐雾测试最高可达120小时)表面可电镀。
压铸件二次加工可控制无砂孔,不渗水,不漏气,产品可氧化各种颜色,不起泡,无水纹,电镀无麻点,同时过酸性盐务96小时达十级,散热性能达200以上。
欢迎来电咨询!
业务咨询:QQ:1556039810 微信/手机:13686609610
技术交流:QQ: 740389501 微信/手机:13829212466
公司官网:http://www.yf5189.com/