锌合金压铸件电镀质量难控制是电镀行业多年来一直存在的老大难问题,通常从原材料生产到开模压铸毛坯,到抛光再到电镀成品往往不在同一个企业中完成,又出于商业竞争的原因,对这个问题的看法,分析众说纷纭没有定论。本文认为毛坯件除了要控制锌材的成份还要控制皮下针(气)孔的深度、大小及分布,皮下浅层针(气)孔会导致电镀膜层厚度减薄组织粗大。在现今制毛坯工艺无法完全消除皮下针(气)孔的情况下,必须使皮下针(气)孔更细更散更深。微孔铬这一电镀工艺是弥补锌合金压铸件存有皮下针(气)孔这一缺陷的最好选择。
【关键词】 皮下针(气)孔 抛光 镀层膜厚 镍封 微孔铬密度
锌合金压铸件可一次成型,产品尺寸精度高,表面质量好,生产效率高,特别是对形状复杂和机械加工难度大的零件,既方便有效,成本费用也较低。所以在卫浴龙头各式样的把手中被广泛采用。锌合金压铸材料大多数选用GB/T 13821-2009标准中YX040A。材料中主要成份是锌,其标准电极电位为-0.76V,化学性质相当活泼,表面硬度低,在运输保管使用中表面极易腐蚀和撞伤,失去光泽,降低美观度,缩短使用寿命。对锌合金压铸把手进行表面装饰防护是市场的必然需要。
卫浴行业特别讲究美观,北美和欧洲市场中高档产品质量要求符合ASTM G85标准中48小时酸性盐雾通过(10级)无缺陷测试。这就给锌合金压铸把手的电镀质量控制带来很大的难度。
对压铸毛坯件质量要求:
第一,采购优质锌锭,存放保持干燥、清洁,熔炼不得混入退镀品、污脏水口料。第二,压铸毛坯无缺料、无变形、无缩水、无起泡无脱皮、无隔层无裂纹、无气孔、无飞边。第三,表面干净无油渍,无碰撞伤痕。第四,经150℃炉箱内烘烤1小时,无起泡。第五,皮下针孔距离抛光表面深度必须大于0.30mm。第六,抛光件密度大于6.58g/cm3。
第一,单独抛光,不得与铜件同场地,同抛光材料。在工件表面若残存有大量铜原子,因为是抛光外力将其侵入,铜原子与锌基体属机械粘连没有扩散互容,在镀碱铜时,必定影响镀层与基体间的结合力和镀层本身的组织结构,从而降低防腐性能。第二,采用红膏粗抛,白膏抛亮,无漏抛,不留坯模痕,表面饱满无凹洼,无凸点,无针孔眼,无黑点。第三,勤上腊,上量少,不大力抛光,避免工件表面高温烧伤产生密集小孔。第四,不过量抛光,余量控制在0.10以内。不允许抛去致密层露出密集针孔眼。第五,单独摆放在干燥、清洁处,不撞碰,避免表面氧化,水化,抛后在尽短时间内进行电镀。
皮下浅层气孔针孔对电镀膜层厚度组织性能影响的微观分析:
以(图1)工件皮下无针孔(或气孔),抛光后表面平整光滑、饱满,在进入镀液后,工件表面分布着均匀的稳定的电场强度,阳离子可以均匀地沉积在表面上,获得组织致密膜厚均匀致密的铜层、镍层和铬层如(图3)所示。
(图2)工件皮下浅层有针孔(或气孔),抛光后表面有很小的凹洼(下方隐藏气孔A,针孔是缩小化的气孔),无光亮感。在镀时,由于气孔的不规则性致工件表面的电场强度变小(电力线变疏),变方向,从阳极到工件表面沉积的铜离子(镍离子,铬离子)相对图1变少而且变方向,会与周围的沉积离子发生干扰,大大减少了阳极离子在凹洼中心区域的有效沉积。这种情形发生在镀铜、镍(含多层镍)铬中,最后所得工件的镀层如图4所示,中心点镀层极薄,各镀层的组织结构也相对粗大,在做酸性盐雾测试时,它又是一个存液穴,特别不耐腐蚀。在经酸性盐雾测试后,会发现工件表面有许多可见的白点,且可用软布擦去,就是典型的皮下浅层气孔(针孔)的电镀表现。假设针、气孔的大小范围为0.05~0.30mm,影响膜层严重的区域约为A的2/3,即B=2/3*0.05~0.30mm,约为0.03~0.20mm。而库仑法测膜厚取用域直径为1.2mm,极薄膜区仅为可测区的1/6以下。因此靠库仑测膜厚法不能发现这一问题。
皮下浅层气(针)孔是影响锌合金压铸件电镀质量(正品率)最基本的最主要的最顽固的缺陷。就现市场的压铸技术能力要完全消除气孔针孔还做不到,可以控制的只是气孔(针孔)的细少化、弥散化、皮下更深化,皮下针孔气孔的可探测性差,往往都采用抛光后凭肉眼全检把关,这就要求检验人员需具有极高的专业化水平和眼力,根据失效模式分析相关理论,凭肉眼检验的可检测度顶多也只有0.5。这是它的基本性和主要性。当皮下气孔或针孔比较弥散,尺寸较小,而且也较深(比如0.50以下),则对电镀层质量的影响也较小。当皮下气孔或针孔稍大些,尺寸也一般(比如0.20mm以下),而且也不算很浅(比如0.20mm左右),则可通过镀了酸铜之后再抛亮一次,对凹洼处进行抛修,去除表皮粗糙组织再进行镀镍镀铬,同样可以通过48小时的酸性盐雾测试,从而提高压铸件利用率。普通的皮下气孔、针孔也可以做出一部份合格的产品的事实,掩盖了皮下气孔针孔的部分危害,构成了顽固性。
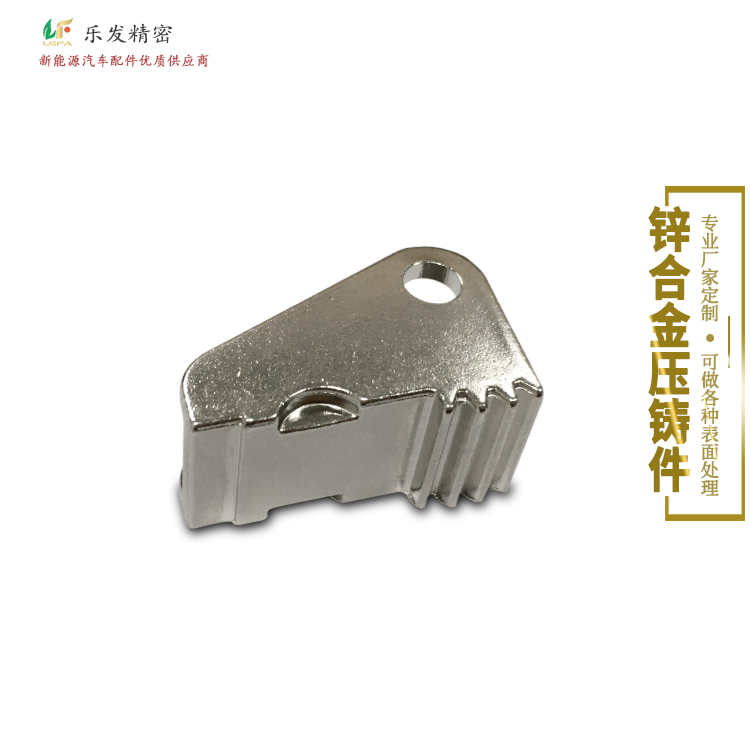
底层镀铜采用氰化镀铜加焦磷酸盐镀铜加硫酸盐光亮镀铜的工艺。
选择半光亮镍+光亮镍+镍封这类镀镍工艺
半光亮镍:在具有良好导电性和覆盖能力的瓦特镍液中加入适当的不含硫的光亮剂,组成半亮镍镀液,与光亮镍层之间产生适当的电位差(80mv~130mv)达到电化保护之目的。半亮镍层膜厚可控制在2/3总膜层(约10μm左右)较为理想。光亮镍:膜层厚度占总镍层厚约1/3左右(即5μm左右)。二层间产生的电位差使得双层镍由单层镍的纵向腐蚀转变为横向的腐蚀,达到保护铜层及以下锌合金基体的作用。镍封:在普通的光亮镍溶液中,加入某些非导体微粒,微粒直径在0.1~1μm(微米)的不溶性固体如SiO2等,通过搅拌使这些微粒悬浮在镀液中,在适当的共沉积促进剂帮助下,使这些微粒与镍发生共沉积而形成镍与微粒组成的复合镀层。在后续镀铬时,由于复合镀层表面上的微粒不导电,铬不能在微粒表面沉积,使铬层上形成大量微孔,即所谓微孔铬。镍封层的微粒密度在1.5万~3万/Cm2最为理想。微孔铬表面存有的大量微孔,可在很大程度上消除普通铬层中的内应力,因而减少了铬层的应力腐蚀,尤为重要的是铬层上的大量微孔将铬层下面的光亮镍大面积地暴露出来,在腐蚀介质作用下,铬与镍组成电池,铬层为阴极,微孔处暴露的光亮镍为阳极而遭腐蚀。从而改变了大阴极小阳极的腐蚀模式,使得腐蚀电流几乎被分散到整个光亮镍层上,从而防止了产生大而深的直贯基体金属的少量腐蚀沟纹和凹坑,并使镀层的腐蚀速度减小,且向横向发展,因而保护了基体,显著地提高了镀层的耐腐蚀性能。
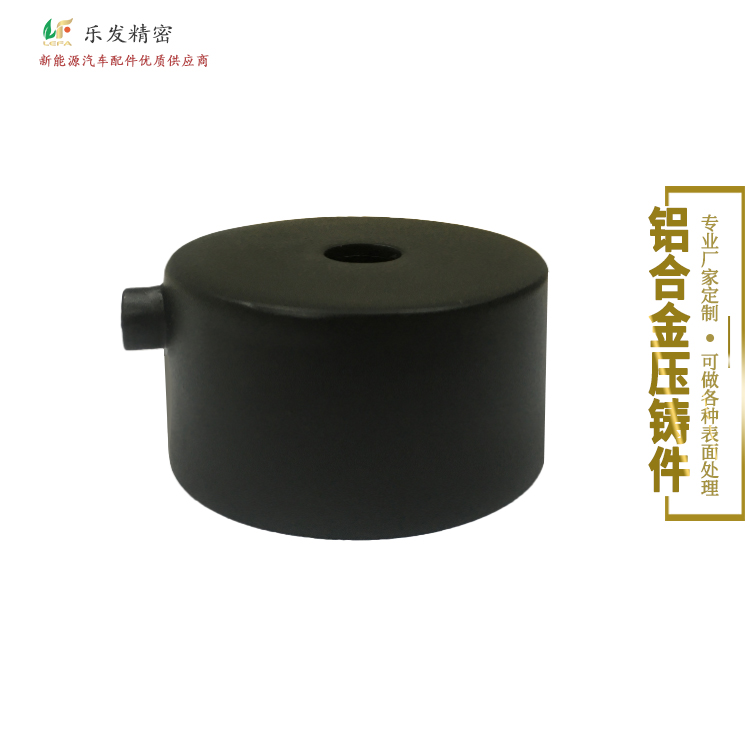
镀铬:为了达到外观光亮,具有良好耐磨性能要求的防护装饰性亮铬层,对外形较复杂的锌合金压铸工件要带电下槽,用1.5~2倍冲击电流20~30S便可获得厚为0.25~0.75μm亮铬层。
锌合金压铸件皮下针孔气孔的广泛存在性决定了微孔铬工艺是锌合金压铸件电镀中几乎成了不二的选择。而微孔铬孔数的正确读数对镍封槽液的维护和控制有着直接的指导作用。
(附图3.10-3),已知M600:1,直径Φ0.34。通过《金相图像分析系统》软件可测量计取微孔铬直径:30μm~10μm,孔数22颗,100/0.0907*22=24255颗/Cm2,4处粘连粘连度4/22*100%=18%,该情形显示除加强搅拌减少粘连其它良好。酸性盐雾测试结果证明耐腐蚀性能好。
除以上所述各种因素的控制之外,电镀挂具的设计及操作要排除工件的压气和换槽时带液窜槽的问题也很重要。